Navigating PFAS Restrictions in Hydrogen Electrolysis with SGen-I
- Mitra Nikpay
- May 16
- 3 min read
Updated: 4 days ago

© [16.05.2025] Dr. Mitra Nikpay and SATOORNIK UG. All rights reserved.
By : Dr.-Ing.Mitra Nikpay
Introduction
The European Union’s ambitious goal to produce 25 million tons of green hydrogen by 2030 drives the rapid deployment of proton exchange membrane (PEM) electrolyzers. These systems rely heavily on per- and polyfluoroalkyl substances (PFAS), particularly fluoropolymers, for their chemical resilience and proton conductivity. However, mounting environmental and health concerns surrounding PFAS have prompted regulatory scrutiny. In January 2023, five European countries proposed a near-total ban on PFAS, including fluoropolymers, to the European Chemicals Agency (ECHA). While temporary exemptions exist for applications lacking alternatives, such as electrolyzers, their long-term viability is uncertain.
Although fluoropolymers are considered non-degradable in their manufactured form, degradation processes during production, operation, and recycling may release environmentally persistent PFAS compounds. These emissions can occur through product water, aerosols, or waste streams during fuel cell operation and end-of-life recycling, particularly due to membrane and catalyst layer breakdown.
Current literature recognizes more than six million PFAS variants. In fuel cells, the widely used perfluorosulfonic acid (PFSA) membranes contain PTFE backbones which are highly susceptible to radical-induced degradation. These degradation pathways can release membrane fragments into the product water. Additionally, PTFE coatings and even nanoparticles used in various layers of the membrane electrode assembly (MEA) can become secondary PFAS emission sources.
Degradation is often initiated by highly reactive free radicals, generated during hydrogen oxidation, oxygen reduction reactions, or the decomposition of hydrogen peroxide, all common phenomena under standard fuel cell operating conditions. Once these radicals attack the PFSA membrane, both the backbone and side chains can be cleaved, leading to the release of fluorinated compounds. While sealing materials like silicone rubber and EPDM are fluorine-free, the membrane remains the primary source of PFAS emissions in PEM systems [1].
At the same time, these same particles, whether generated internally or introduced via feedwater, can disrupt the membrane’s function by accumulating on its surface or within its structure. This interference impairs proton conductivity, accelerates membrane degradation, and ultimately compromises hydrogen production efficiency. This clogging can be about 40% of the membrane efficiency. Thus, the issue is not only the release of persistent contaminants but also their detrimental impact on system performance [2].
Recognizing the gravity of this issue, researchers are exploring PFAS-free alternatives and radical scavengers to enhance material durability. Yet, replacing the carbon-fluorine bond — one of the strongest in chemistry, remains a formidable challenge [3].
At SATOORNIK, we view this not just as a materials challenge but as a water systems problem. Our SGen-I technology offers an innovative, chemical-free solution to ensure ultra-pure water for PEM electrolyzers. By preventing the accumulation and recirculation of micropollutants and PFAS degradation byproducts, SGen-I safeguards both system performance and environmental compliance, enabling the hydrogen sector to grow responsibly and sustainably [4].
Key Advantages of SGen-I:
Ultra-Pure Water Protection: Maintains electrolyte integrity without chemical leaching.
Membrane Longevity: Extends the lifespan of PEM/Nafion membranes under high-demand cycles.
Energy Efficiency: Optimizes power-to-hydrogen conversion rates.
PFAS and Micropollutant Capture: Effectively removes PFAS, microplastics, and biopolymers without additives.
Non-Invasive Integration: Seamlessly retrofits into existing systems without chemical risks.
Compact and Silent Operation: Designed for minimal footprint and noise-free performance in both laboratory and industrial settings.
Circular Design: Supports closed-loop hydrogen systems, promoting sustainability.
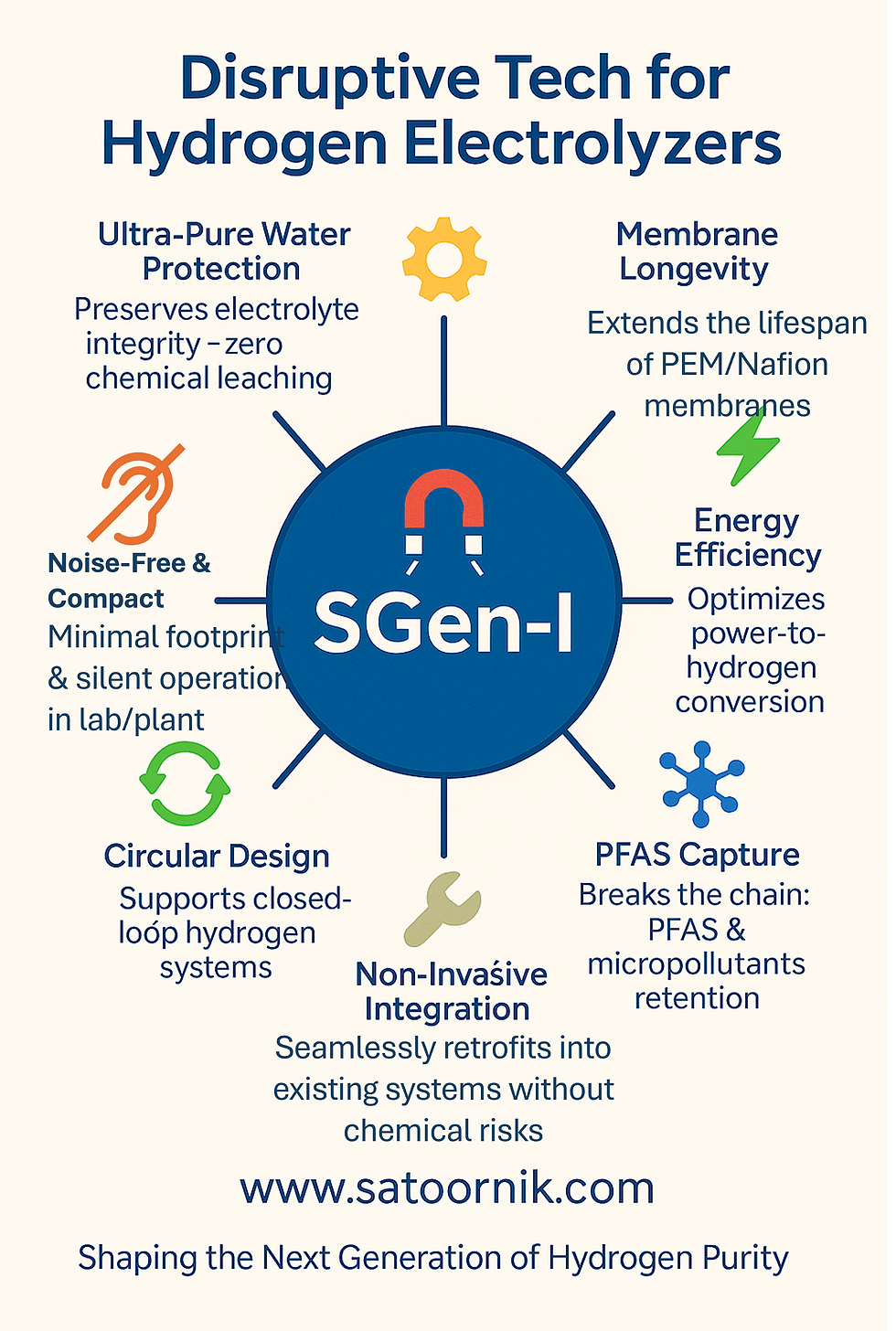
A Strategic Partner for the Hydrogen Economy
SGen-I helps bridge the gap between today’s high-efficiency electrolyzer technologies and tomorrow’s regulatory and sustainability requirements. By purifying water both upstream and downstream of the electrolyzer stack, the heart of hydrogen production, our solution enhances system resilience and long-term reliability. It does so without chemicals, without operational downtime, and without compromise.
Hydrogen's future relies not only on clean energy, but also on clean water. We're proud to make both possible.
References:
1. von Tettau, P., Thiele, P., Mauermann, P., Wick, M., Tinz, S. and Pischinger, S., 2025. Per-and polyfluoroalkyl substances in proton exchange membrane fuel cells—A review. Journal of Power Sources, 630, p.236104.
2. Enfrin, M., Wang, J., Merenda, A., Dumée, L.F. and Lee, J., 2021. Mitigation of membrane fouling by nano/microplastics via surface chemistry control. Journal of membrane science, 633, p.119379.
3. Sinha, P. and Cypher, S.M., 2024. Life Cycle Fluoropolymer Management in Proton Exchange Membrane Electrolysis. Hydrogen, 5(4), pp.710-722.
4. Nikpay, M. and Toorchi Roodsari, D., 2025. Magnetic Field Induced Changes in Surface Tension in Pure Water and Polystyrene Micro-Nanoparticle Dispersions. Pollution. 10.22059/poll.2025.388248.2731
Contact us: info@satoornik.com
Comments